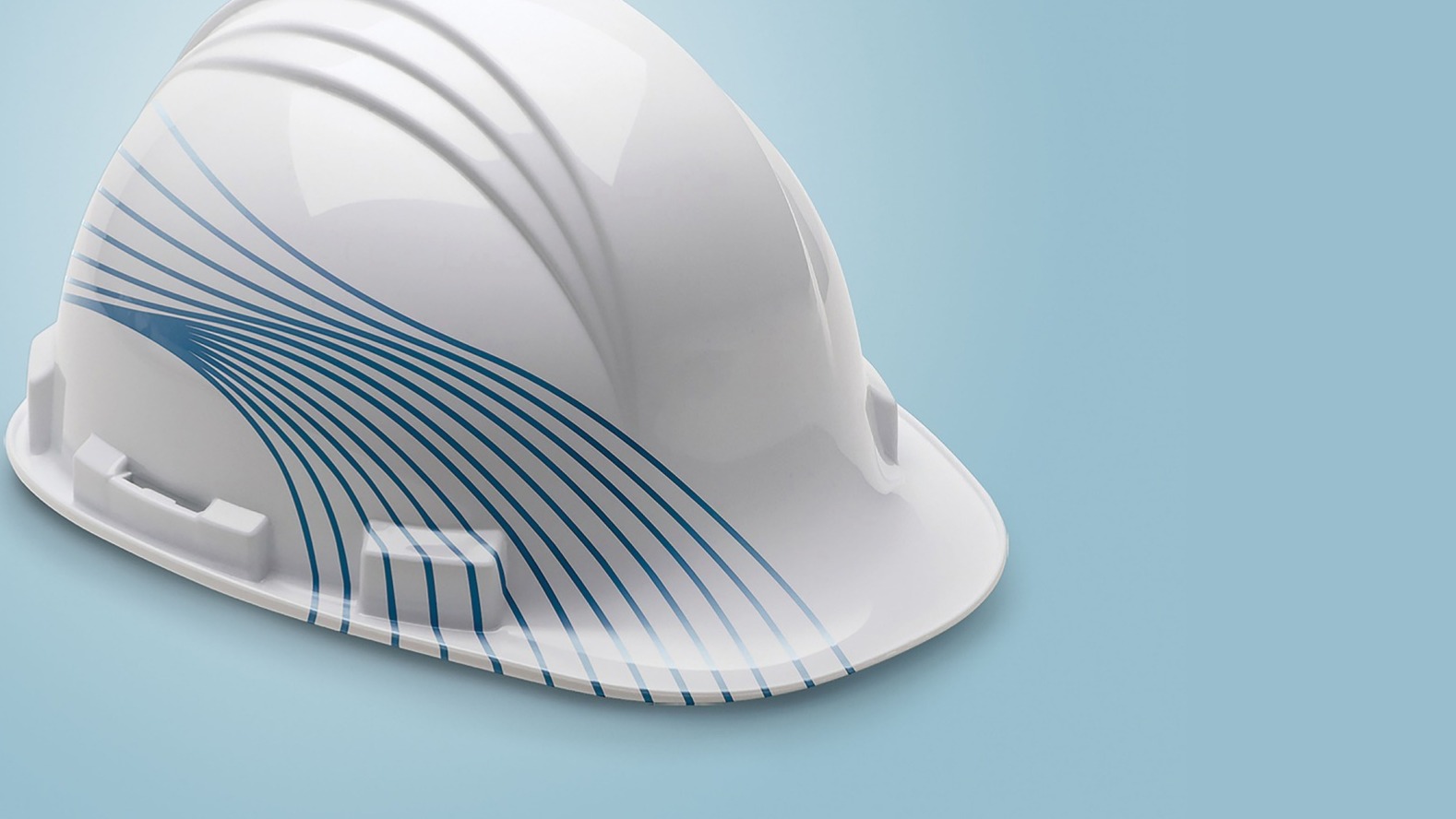
Installation Issues Insulation Contractors Encounter
Top 10 Installation Issues Insulation Contractors Encounter
Table of Contents
- Introduction
- 1. Insufficient Coverage
- 2. Air Leakage
- 3. Moisture Management
- 4. Improper Installation Techniques
- 5. Compression and Settling
- 6. Inadequate Airflow Considerations
- 7. Inadequate Insulation for Specific Areas
- 8. Insufficient Fire Safety Measures
- 9. Poor Quality Control
- 10. Lack of Proper Training and Certification
- FAQs
Introduction
Insulation plays a vital role in enhancing energy efficiency, comfort, and indoor air quality in residential and commercial buildings. However, insulation installation is a complex process that requires skill and expertise. Insulation contractors often encounter various challenges and issues during the installation phase. In this article, we will explore the top 10 installation issues insulation contractors may face and discuss ways to address them effectively.
1. Insufficient Coverage
Insufficient coverage occurs when insulation is not applied uniformly or adequately across all areas of a building. Gaps, voids, or missed spots can compromise the insulation's effectiveness and result in energy loss and reduced thermal performance. To overcome this issue, contractors must meticulously inspect and ensure proper coverage during the installation process. Utilizing proper techniques, equipment, and ensuring a thorough application can help minimize the risk of insufficient coverage.
2. Air Leakage
Air leakage refers to the uncontrolled movement of air through gaps or cracks in the building envelope. Air leaks can undermine the insulation's ability to prevent heat transfer and can lead to energy waste and discomfort. Contractors should conduct a thorough air sealing process before installing insulation to minimize air leakage. Properly sealing gaps, cracks, and joints with appropriate materials such as caulk or weatherstripping helps create an airtight envelope, enhancing the insulation's performance.
3. Moisture Management
Moisture management is a critical aspect of insulation installation. Failure to address moisture issues can lead to mold growth, deterioration of insulation materials, and compromised indoor air quality. Insulation contractors need to identify potential moisture sources and take necessary precautions during installation. Implementing proper vapor barriers, addressing water leaks or condensation issues, and ensuring adequate ventilation are essential steps to prevent moisture-related problems.
4. Improper Installation Techniques
Using incorrect installation techniques can significantly impact the performance and longevity of insulation. Each insulation material has specific installation requirements that must be followed for optimal results. Insulation contractors should be well-versed in the proper techniques and guidelines provided by manufacturers. This includes understanding proper handling, cutting, fitting, and fastening methods for different insulation materials. Following industry best practices and manufacturer instructions ensures that insulation is installed correctly and achieves the desired outcomes.
5. Compression and Settling
Compression and settling are common issues with certain types of insulation materials. Over time, insulation may compress or settle due to gravity, vibration, or other factors. This can reduce the insulation's thickness and its ability to provide effective thermal resistance. Insulation contractors should be aware of the potential for compression or settling and take appropriate measures to mitigate it. This may involve using materials with higher resilience, installing additional insulation to compensate for anticipated settling, or employing techniques to prevent compression, such as providing adequate support during installation.
6. Inadequate Airflow Considerations
Proper airflow is crucial for maintaining good indoor air quality and preventing moisture-related issues. Insulation contractors must consider the impact of insulation on ventilation systems and airflow patterns within the building. Blocking or obstructing airflow vents, soffits, or other ventilation pathways can lead to restricted air movement and potential issues with condensation. Contractors should ensure that insulation installation allows for proper airflow and consult with HVAC professionals if necessary.
7. Inadequate Insulation for Specific Areas
Different areas of a building may require different types or levels of insulation based on their unique characteristics. Insulation contractors should assess and determine the appropriate insulation materials and R-values for each specific area. For example, attics, walls, floors, and basements may have different insulation requirements. Failing to provide adequate insulation in certain areas can result in energy inefficiency and compromised comfort. Proper planning and customization of insulation solutions based on the building's needs are crucial to avoid this issue.
8. Insufficient Fire Safety Measures
Fire safety is a critical consideration when installing insulation, especially in commercial buildings or multi-unit residential properties. Insulation materials should meet the required fire safety standards and codes to ensure occupant safety. Contractors must select and install insulation products with appropriate fire ratings and provide adequate fire barriers or enclosures as necessary. Adhering to fire safety regulations helps protect the building and its occupants in the event of a fire.
9. Poor Quality Control
Maintaining strict quality control throughout the insulation installation process is essential for achieving desired outcomes. Insulation contractors should establish robust quality control measures to ensure that installations meet industry standards and best practices. This includes thorough inspections, proper documentation, and addressing any deviations or deficiencies promptly. Implementing a quality assurance program helps minimize errors and ensures that the insulation performs as intended.
10. Lack of Proper Training and Certification
Insulation installation requires knowledge, expertise, and awareness of the latest industry practices and advancements. Contractors should invest in continuous training and education to stay updated with new insulation technologies, installation methods, and building codes. Obtaining relevant certifications and affiliations demonstrates a contractor's commitment to professionalism and competence. Customers should prioritize working with contractors who possess the necessary training and certifications for insulation installation projects.
By addressing these common installation issues, insulation contractors can enhance the effectiveness and performance of insulation systems, ensuring optimal energy efficiency, comfort, and durability for buildings.
FAQs
Q: How can I choose a reliable insulation contractor?
A: When selecting an insulation contractor, consider their qualifications, experience, reputation, and certifications. Request references, review their portfolio, and ask about their training and credentials related to insulation installation. It's also essential to obtain detailed proposals and contracts that clearly outline the scope of work.
Q: What are some signs of improper insulation installation?
A: Signs of improper insulation installation include uneven temperatures throughout the building, drafts or air leaks, high energy bills, moisture issues, and reduced indoor comfort. If you notice these signs, it's advisable to have a professional insulation contractor assess the installation and address any issues.
Q: How long does it take to install insulation in a commercial facility?
A: The installation duration depends on various factors, such as the size and complexity of the facility, the insulation material used, and the scope of work. Commercial insulation projects can range from several days to several weeks or more. It's recommended to consult with an experienced insulation contractor to determine a more accurate timeline based on your specific project.
Q: What should I do if I suspect insulation issues in my building?
A: If you suspect insulation issues in your building, contact a professional insulation contractor for an inspection. They will assess the installation, identify any problems, and recommend suitable solutions. Timely action is crucial to ensure optimal energy efficiency, comfort, and indoor air quality.
Q: Can insulation contractors address specific insulation needs for different areas of a building?
A: Yes, insulation contractors can assess the specific needs of different areas in a building and recommend suitable insulation solutions. They consider factors such as the area's location, purpose, and insulation requirements to provide customized solutions that meet energy efficiency and comfort goals.